Cor-Pro Systems, Inc. is the leading provider of corrosion testing services in Houston, Texas and nearby Gulf Coast areas.
Proper assessment of the life and integrity of an equipment is possible through corrosion testing Houston.
Corrosion testing helps in the identification of applicable corrosion allowance and in the evaluation of the environmental impact of corrosion.
To determine the inherent corrosivity of the component, it is necessary to subject the material in a particular environment.
The process of corrosion testing involves getting a representative sample of the component and exposure to an environment that closely resembles the environment of interest.
Corrosion testing is often used in assessing a material’s ability to withstand environmental conditions.
Cor-Pro’s corrosion testing Houston services are among the most trusted because of the thorough performance of the company’s NACE-certified corrosion experts.
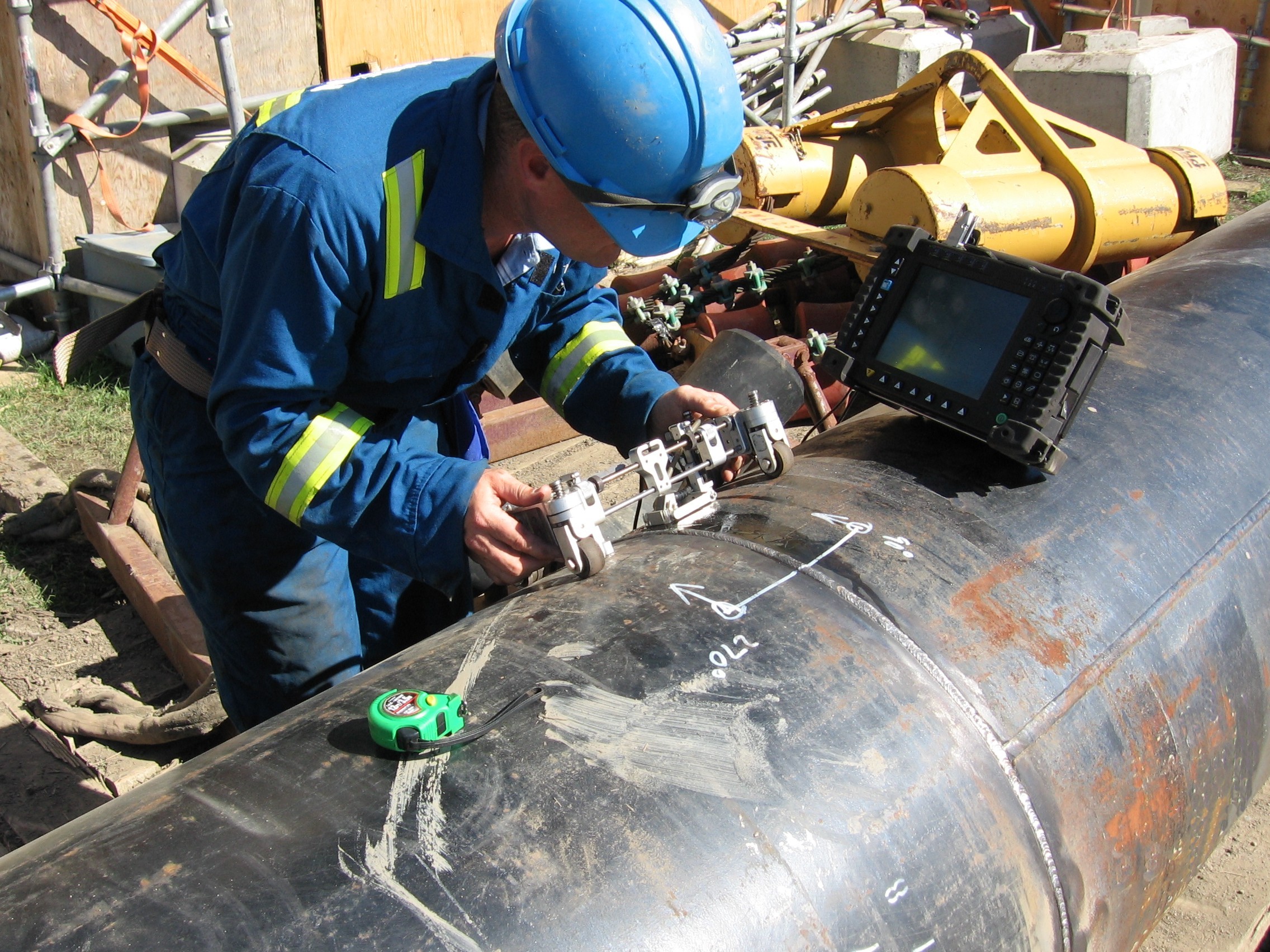
Cor-Pro Systems, Inc. recommends proper corrosion testing as part of their mission of increasing awareness about corrosion, its negative effects, and the effective ways to mitigate it.
Read about Cor-Pro’s Corrosion Testing Houston services to help you decide on which corrosion management best suits your needs.
Main Types Of Corrosion
Corrosion testing has several methods, each assessing a particular type of corrosion. Corrosion types include:
- General Corrosion
- Localized Corrosion
- Environmentally assisted cracking (EAC)
- Microbiologically influenced corrosion (MIC)
Oftentimes, test result interpretation is not straightforward. Aside from the result, analysts have to consider the type of test used and design parameters of the simulated system, as well.
For instance, corrosion allowance depends on the function of the component, the desired and expected life span, and design restrictions.
Methods Of Corrosion Testing Houston
Evaluation Of General Corrosion
General corrosion typically occurs as a uniform degradation of material from environment-wetted surface of a component. It is noticeable that as the surface continues to corrode, the component thins out.
This is problematic for components used in pressure-containing and load-bearing equipment.
For example, the flowlines that normally undergo general corrosion have designs that come with a corrosion allowance calculated based on general corrosion test results and the desired service life of the flowline.
To properly assess it, analysts fabricate a representative coupon of the material, which are rectangular in shape and measures about 1” to 2” on each side and is about 1/8” in thickness.
After measuring and weighing the coupons, testers will expose the material to the test environment. Exposure time is dependent on the design life of the component, and can sometimes last from days to months.
As soon as exposure time is up, the coupon undergoes reweighing and re-measuring. To properly calculate the corrosion rate, analysts use a standard formula that incorporates the surface area, mass, density, and exposure time of the material.
Reporting of corrosion rate is in mm/year or mils/year (mpy), where one “mil” is equivalent to 1 milli-inch.
Evaluation Of Localized Corrosion
Localized corrosion comes in two common forms:
1. Pitting Corrosion
In this form, the corrosion stays localized into a small surface, but it can penetrate deeper and faster into the component’s diameter.
Coupons or tensile specimen surface with pitting corrosion are easily identifiable by simple visual inspection.
2. Crevice Corrosion
Crevice corrosion, on the other hand, happens when fluid cannot flow or remains stuck in or between components. They are more commonly seen around nuts and bolts, underneath washers and disbanded coatings.
Testing for susceptibility of crevice corrosion is by clamping plastic washers to samples of the material, then putting these assemblies into a chosen environment.
Localized corrosion and its severity evaluation depend on the penetration depth of the pits and crevices and the material size.
Evaluation Of Environmentally Assisted Cracking (EAC)
Corrosion engineers consider EAC as the most dangerous from of corrosion because of its potential to cause catastrophic component failure, and because it is often undetected via non-destructive evaluation methods.
Cracking occurs when a susceptible component undergoes environmental stress. EAC includes:
- Sulfide Stress Cracking (SSC)
- Stress Corrosion Cracking (SCC)
- Hydrogen Induced Stress Cracking (HISC)
The inherent vulnerability to EAC is reliant on the environment surrounding the material. For example, Titanium goes through hydrogen embrittlement in an environment with methanol. Carbon steel, on the other hand, undergoes cracking in environments rich in acidic-sulfide.
To properly apply corrosion testing and EAC susceptibility of a material, application of stress during testing is necessary. As described by NACE TM0177, the test methods are commonly used for:
- Fitness-For-Service (FFS)
- Material Qualification
- Quality Assurance
Evaluation Of Microbiologically Influenced Corrosion (MIC)
Components exposed to an environment with significant bacteria growth on a prolonged period develop corrosion. One example is a stagnant environment that aggravates the MIC.
For example, sulfate reducing bacteria (SRB) can gather in trapped waters in the corners of a carbon steel tank. The bacteria will cut the sulfate present in the water and form hydrogen sulfide gas that promotes corrosion.
The presence of MIC is verifiable by conducting extensive corrosion testing of the fluids produced in contact with the component.
Assessment includes placing of coupons of the component in the process stream where MIC is. Evaluation is through microbiological techniques such as fluorescence microscopy.
Corrosion Testing Houston Through Cor-Pro Systems, Inc.
Prior to application of corrosion coatings, Cor-Pro performs through corrosion testing to properly identify the offending agent and choose the appropriate coating systems.
Cor-Pro’s has corrosion monitoring to aid corrosion testing. This includes:
Non Destructive Testing Analytical Chemistry
- Eddy current/magnetic flux
- Intelligent pigs
- Radiography
- Thermography
- Ultrasonic testing
Operational Data
- Flow rate (velocity)
- pH
- Pressure
- Temperature
Corrosion Monitoring
- Electrical resistance
- Galvanic current
- Hydrogen penetration
- Linear polarization
- Weight loss coupons
Fluid Electrochemistry
- C. impedance
- Potential measurement
- Potentiodynamic measurements
- Potentiostatic measurements
Data gathered through these corrosion testing will give a useful information about the corrosion process. This is vital in the formulation of corrosion protection methods.
About Cor-Pro Systems
Cor-Pro has close to 30 years of experience with providing unsurpassed corrosion protection services to several clients enabling the company to deal with hundreds of corrosion issues.
Further, this helped the company in developing and formulating reliable and cost-effective corrosion prevention and control systems.
Cor-Pro’s extensive and thorough corrosion testing made them the company of choice in Houston, Texas and areas near the Gulf Coast.
Get Thorough Corrosion Testing Houston Through Cor-Pro Systems, Inc.
If you have questions about our corrosion testing Houston services or want to get a custom quote for your particular corrosion protection need, contact us at 713-896-1091, or send us an e-mail at quotes@cor-pro.com.