Cor-Pro Systems provides top-of-the-line corrosion protection of metals services in Houston, Texas and nearby Gulf Coast areas.
To properly apply corrosion protection of metals, it is important to understand how corrosion occurs. For corrosion to happen, these three things should be present:
- Two different metals (i.e. steel and aluminum)
- A metal conducting path in between the two different metals
- An electrolyte (i.e. water with dissolved salt)
Once these conditions are present, corrosion is inevitable. It is a natural phenomenon that destroys metals either through an electrochemical or chemical reaction.
Cor-Pro commits to provide industries and its stakeholders the optimum service when it comes to corrosion protection. The company strives to give useful information about corrosion, its negative effects, and how to effectively mitigate it.
Cor-Pro specializes in corrosion protection of metals. The company has a team of NACE-certified professionals that work cohesively to give the clients the superior corrosion protection for their corresponding industries.
Read about Cor-Pro’s Corrosion Protection Of Metals and find out the methods ideal for your corrosion needs.
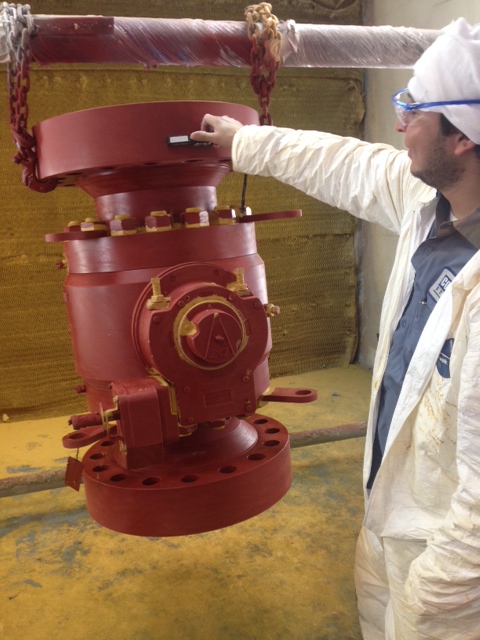
Types Of Corrosion Protection Of Metals
About 15 million known chemicals (organic and inorganic) cause corrosion. Corrosion engineers believe that applying the correct corrosion protection of metals is crucial to achieve optimum corrosion protection.
At present, two methods of corrosion protection of metals are widely applied by corrosion experts. Cathodic protection and chemical inhibitors both depend on adjusting the charge present on the metal surface – identified by measuring the potential of the metal.
Corrosion Protection Of Metals Through Chemical Inhibitors
Chemical inhibition works by eliminating the electron. Removal of electrons results to forcing the potential towards the positive region where the oxide film will spontaneously form. When this happens, the metal surface becomes stable and passive with a low rate of corrosion.
This corrosion protection of metals is typically applied as internal protection of carbon steel pipes and vessels. It is an economically preferred method to use over stainless steel alloys, non-metallic composites, or coatings. It confers protection without disrupting an on-going process.
Industries that benefit from this metal corrosion protection method include:
- Oil and gas exploration and production
- Chemical manufacturing
- Petroleum refining
- Water treatment
- Heavy manufacturing
- Product additive industries
In the recent study initiated by NACE International, corrosion inhibitors cost the U.S. economy about $1.1 billion in 1998, double the amount spent in 1982 which cost roughly $600 million. This data reiterates the need for protection of metals against corrosion.
Corrosion Protection Of Metals Through Cathodic Protection
Cathodic protection works by pushing the potential of the metal to a negative region where the metal is highly stable. This simply means that the active (anodic) sites present on the metal surface convert to passive (cathodic) sites.
This is achieved by using a sacrificial anode composed of a more reactive metal, or by increasing the charge of the metal surface by applying an electric current.
Sacrificial anodes are more active compared to steel. These galvanic anodes “sacrifice” themselves to protect the metal against corrosion.
How To Know If Cathodic Protection Is Enough
As the current flows onto a metal surface, it normal potential shifts towards the negative direction. To find out whether the metal has sufficient protection, obtaining the metal potential is necessary. This metal potential is then measured against a standard reference electrode.
When there’s enough current to polarize or shift the potential to a negative value, corrosion protection of metals is sufficient. The values should be as follows:
- -850 mV versus a Cu/CuSO4
- -800 mV versus a Ag/AgCl
- +250 mV versus Zn
Ideally, Ag/AgCl and Zn standard reference electrodes are for sea water measurements, while Cu/ CuSO4 are more commonly for buried services measurements.
Corrosion Protection Of Metals By Cor-Pro Systems, Inc.
Cor-Pro Systems offers superior corrosion protection of metals through:
- Epoxy Coatings
- 1-Hour Cure Epoxies
- Urethane Coatings
- Zinc Primers
- Enamels
- Thermal-Cured Thin Film (Xylan, Ceramic, Metallic, Thin Film Epoxy Moly, etc)
- Wear-Resistant Coatings
- High Temperature Coatings
- Abrasive Blasting (complete line of abrasive media available)
- Alternative profile achievement for areas not allowing blast
Cor-Pro Systems recently received certification from the internationally accepted OHSAS 18001:2007 Occupational Health and Safety Management Systems from Verisys Regsitrars.
About Cor-Pro Systems
With close to 30 years of experience in the corrosion protection industry, Cor-Pro can solve any corrosion issue at hand. Additionally, Cor-Pro aims to raise awareness about the corrosion and its detrimental effects to the economy and the environment.
Cor-Pro adheres to international guidelines to provide its clients high quality service that the company is known for.
Get The Best Corrosion Protection Of Metals Through Cor-Pro Systems, Inc.
If you have questions about our corrosion protection of metals or want to get a custom quote for your particular corrosion protection need, contact us at 713-896-1091, or send us an e-mail at quotes@cor-pro.com.
Explore our Velocity Service page to know more about our personalized corrosion protection systems.