Cor-Pro Systems is the leading provider of subsea pipeline corrosion protection services in Houston, Texas and nearby Gulf Coast areas.
Since 1948, the Gulf of Mexico has over 24,000 miles of pipeline. Through the years, most of these pipelines were intentionally removed or abandoned, and as of June 1997, there exists about 17,000 miles of operational pipes. To date, some 1,222 miles of these pipes are more than 30 years old while about 5,952 miles are on their second decade already.
Based on these numbers, almost 8,000 miles of pipes have poor integrity and are at a higher risk of leaks and damages.
Malfunction at any point of the pipeline can cause oil leaks that have damaging effects on the marine environment and severe financial consequences for the owner.
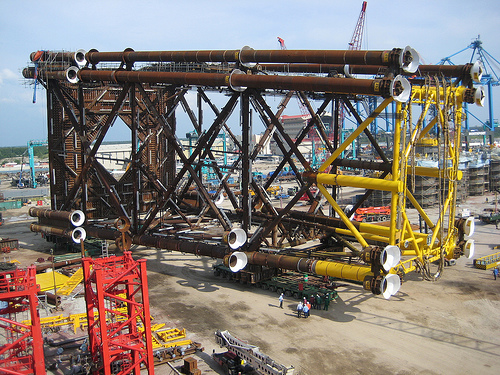
Cost based and technical considerations carried out at the outset of planning and design can give log-term benefits in terms of integrity and safety of the subsea pipeline.
Subsea pipeline corrosion protection is an integral part of asset protections. It is important that submerged pipelines have anti-corrosion coatings applied on external surfaces.
External Corrosion Control Of Subsea Pipelines
All subsea pipelines have protection from saltwater corrosion in the same way. The main corrosion control system used is pipeline coating. Cathodic protection (CP) supplements the surface coating to give protection at coating defects, also known as “holidays.” At present, the trend is to use fusion-bonded epoxy powder coatings (especially in pipelines found in the Gulf of Mexico).
Almost all newly installed pipelines in the Gulf of Mexico use aluminium bracelet anodes.
Two basic types include: square shouldered and tapered.
- Square shouldered anodes are often used on pipes with concrete weight coating. The anodes are slightly recessed inside once installed on the exterior diameter of the concrete.
- Tapered anodes are typically installed on pipelines together with a thin film corrosion coating. This is to offer protection for the bracelet anodes during pipe-laying because the pipes tend to have mechanical damage as it travels over the stinger on the rear of the lay barge.
Designing Cathodic Protection System As A Subsea Pipeline Corrosion Protection Method
Corrosion engineers need to consider the following factors when designing cathodic protection systems:
- Expected design life required (standard minimum is 20 years)
- Geographic location
- Type of coating to use
- Pipe diameter length
- Depth of water
- Burial method
- Pipe-laying/installation method
- Electrical isolation from platforms or other pipelines
- Product temperature
All of these variables have significant impact on the final anode alloy and size selection.
An approved subsea pipeline corrosion protection designer will consider and identify the preferred pipe installation method, as this will have a direct and significant impact on the extent of expected coating damage.
In almost all pipelines design guidelines, the use of conservative approach is necessary. For instance, many of early Gulf of Mexico subsea pipelines have a design basis of 2mA/ft of bare steel and 5% coating failure. In principle, this equates to taking 5% of the overall pipeline surface area and putting 2mA/ft of cathodic subsea pipeline corrosion protection to it.
When thinking about the role of cathodic protection in the integrity of the pipeline, investigation should include the actual causes of subsea pipeline failure and leakages.
Subsea pipelines aged more than 30 years have higher risks of failure and leakages. In fact, the first instance of a leak could be the demise of the subsea pipeline. Due to the cost of subsea pipeline-laying, most of the existing pipelines may not undergo replacement.
Two basic strategies that subsea industries can adopt include:
- Surveying of the subsea pipeline corrosion protection system such as cathodic protection systems
- Retrofitting of the protection system
Use of close-interval cathodic protection surveys are the most rational technique, but rarely used. Accurate survey systems include:
- Physical contact to the pipeline
- Use of remotely operated vehicles (ROVs)
These methods track the pipeline while carrying reference electrode arrays that will assist operators in making informed decisions about retrofitting.
Retrofitting of the subsea pipeline corrosion protection system through the use of supplemental anodes will only be beneficial if the pipeline of interest is old and has a significant additional lifespan because of the associated cost of pipeline inspection.
For this reason, it is highly advised to conduct a thorough pipeline survey beforehand.
Subsea Pipeline Corrosion Protection From Cor-Pro Systems, Inc.
Cor-Pro provides protective subsea coatings through:
- Epoxy Coatings
- 1-Hour Cure Epoxies
- Urethane Coatings
- Zinc Primers
- Enamels
- Thermal-Cured Thin Film (Xylan, Ceramic, Metallic, Thin Film Epoxy Moly, etc)
- Wear-Resistant Coatings
- High Temperature Coatings
- Abrasive Blasting (complete line of abrasive media available)
- Alternative profile achievement for areas not allowing blast.
Cor-Pro Systems, Inc is OHSAS 18001:2007 and ISO 9001:2008 certified. Both certification conferred by Verisys Registrars.
Velocity: Part Of Cor-Pro’s Commitment To The “Cor-Pro Gold Standard”
Subsea pipeline corrosion protection is a necessary requirement for submerged pipelines and it is Cor-Pro’s commitment to deliver only the best corrosion protection methods in Houston and nearby Gulf Coast areas.
All of the company’s products and services are marked with the highest level of corrosion management standard – the “Cor-Pro Gold Standard.”
To ensure all Cor-Pro’s clients receive quick and quality service, each work done follow the “Velocity Seal of Quality” – superior corrosion protection service in just a matter of hours, not days.
About Cor-Pro Systems
Cor-Pro Systems is a company that specializes in subsea pipeline corrosion protection in Houston, Texas and in the Gulf Coast. With close to four decades of experience in various corrosion problems, Cor-Pro remains the company of choice for reliable and trustworthy corrosion protection.
Cor-Pro works with several stakeholders to further improve its personnel training and management practices to continue providing for its clients and partner industries.
The company also invests in continuous research and development to find innovative ways of fighting corrosion.
Get Top-Of-The-Line Subsea Pipeline Corrosion Protection Houston From Cor-Pro Systems, Inc.
For any questions regarding our subsea pipeline corrosion protection systems or want to have a custom quote for your industry, please feel free to call us at 713-896-1091, or email us at quotes@cor-pro.com.