Cor-Pro Systems, Inc. is the leading company of choice for superior subsea corrosion protection services in Houston, Texas and nearby Gulf Coast areas.
Subsea corrosion, particularly on oil and gas pipelines, is a critical problem that can cause catastrophic failure when not managed properly. Proper management of subsea equipment involves careful design and continuous monitoring and maintenance.
Saltwater is among the most potent corrosive agents known today that makes marine industries at a higher risk of having corroded and damaged equipment.
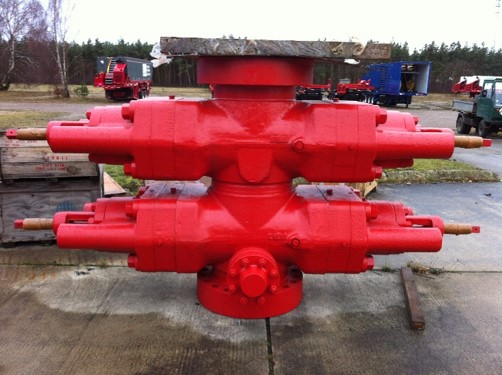
According to experts, most offshore pipeline failures are attributable to internal corrosion. That said, subsea pipelines subjected to harsh seawater environment undergoes even more significant damage due to a number of factors: complexity of design, difficulty of inspection, monitoring, and repair, and heightened internal and external corrosion progression.Over time, comprehension of corrosion along with the mitigation techniques improved; however, significant challenges still persist for the subsea environment.
Cor-Pro serves various industries in need of subsea corrosion protection services for more than 27 years and has become the leading provider in Houston and Gulf Coast areas nearby.
The company, following its mission-vision, gives its clients nothing but the best corrosion protection services that complies with international guidelines and standards.
Learn about Cor-Pro’s Subsea Corrosion Protection in Houston and discover the best corrosion solution suitable for your industry.
What is Subsea Corrosion?
Corrosion is a gradual destruction of materials through its chemical reaction with the environment. Industries in the oil and gas production face the problem of corrosion. Due to constant exposure to the harsh seawater environment, submerged equipment has a higher rate of corrosion.
In cases of subsea operations where explorations move deeper into more hostile waters, the impact of corrosion increases significantly. Subsea corrosion happens rapidly because the seawater turns into a voltaic cell that accelerates the process of corrosion.
Subsea corrosion affects the metal by:
- Anodic action that causes surface pitting of metals
- Cathodic action that makes hydroxide ions by oxygen reduction to the air.
The mitigation of these processes and prevention of further damages associated with corroded equipment are possible through the use subsea coatings.
Subsea pipelines can be several hundred meters long and submerged in varying depths running from platform to platform or platform to onshore facilities.
These pipelines undergo internal corrosion, largely due to sulphate-reducing bacteria (SRB), and tend to have shorter service life. Based in history, this corrosion process resulted to pipeline repairs and replacements as early as four years.
Cost Of Subsea Corrosion
In the often cited 1998 study conducted by NACE, cost of corrosion is approximately $276 billion annually. To update this, the organization did a double take and further scrutinized the figures, accounting for the inflation rate. The updated cost of corrosion now amounts to over $1 trillion annually.
To what extent of this amount relates to subsea corrosion?
The Corrosion Costs Study by the NACE divided the US economy into 5 industries.
- Infrastructure: $22.6 billion
- Production and Manufacturing: $17.6 billion
- Transportation: $29.7 billion
- Government: $20.1 billion
- Utilities: $47.9 billion
Of these industries, a large part of subsea industries are in the production and manufacturing. To further understand the cost of subsea corrosion, production and manufacturing costs are as follows:
- Pulp and Paper: $6 billion
- Food Processing: $2.1 billion
- Home Appliances: $1.5 billion
- Agricultural: $1.1 billion
- Mining: $0.1 billion
- Petroleum Refining: $3.7 billion
- Oil and Gas Exploration and Production: $1.4 billion
- Chemical, Petrochemical, and Pharmaceutical: $1.7 billion
Those directly related to subsea industries include petroleum refining, oil and gas exploration and production, and chemical and petrochemical industries that have an alarming combined corrosion cost of $6.4 billion.
The cost of subsea corrosion includes all the necessary expenses associated with mitigation of corrosion. It can either be direct or indirect costs. Expenses directly attributable to corrosion are direct costs of corrosion. They can be: (1) construction, design, and manufacturing; and (2) corrosion management costs.
Cost of construction, design, and manufacturing are:
- Corrosion allowance
- Corrosion prevention measures costs (equipment, labor, and overhead)
- Material selection
- Protection technologies
Corrosion management costs:
- Corrosion-related inspection, maintenance, and repairs
- Maintenance and inventory of back up components
- Material replacement of corroded parts identified during operation or inspections.
- Operational losses (production time)
- Refurbishment and rehabilitation
By having a well-executed subsea corrosion protection system, the industries can save:
- Petroleum Refining: $1 – $1.11 billion
- Chemical, Petrochemical, and Pharmaceutical: $425 – $510 million
- Oil and Gas Exploration and Production: $350 -$420 million
Subsea Corrosion Protection Benefits From Cor-Pro Systems, Inc.
By availing of Cor-Pro Systems’ specially engineered subsea coatings, subsea industry players will benefit by having:
- Longer equipment service life that translates to increased production output
- Better performing equipment that produces improved product and service quality
- Higher equipment reliability
- Longer machine maintenance interval
- Reduced energy costs
- Increased safety to personnel
- Less environmental damage
Protective Subsea Coatings
Types of Subsea Coatings
Corrosion is inevitable but its inhibition is also plausible through correct application of specially engineered coating solutions to protect against corrosion, prolong service life, and control maintenance costs.
There are numerous ways of subsea corrosion protection, which includes changing the environment through the use of inhibitors, anodic or cathodic protection, and corrosion-resistant coatings. Of these options, corrosion-resistant coatings are the most widely used corrosion protection. These can be metallic, organic, or inorganic.
Subsea coatings are specially formulated to provide protection against the harsh elements of the seawater. Through these coatings, submerged metals can resist the saltwater and have a slower rate of corrosion.
Types of subsea coatings include:
- Bituminous Binders
- Cellulose Derivatives
- Chlorinated Rubber Resins
- Vinyl Resins
Bituminous Binders are oftentimes oils or resins but they can also be inorganic compounds such as self-curing silicates, soluble silicates, or self-curing solvent based silicates.
Binders are usually used in anti-rust paints for production decks and ship hulls.
Cellulose Derivatives are coatings derived from cellulose; like the water soluble corrosion inhibitor, hydroxythylcellulose (HEC).
Cellulose derivatives have a number of adsorption centers that aid in the metal’s formation of ion complexes. These adsorption centers make these polymers the perfect corrosion inhibitor for submerged components.
Chlorinated Rubber Resins are inert resins that have a reduced oxygen and water permeability and higher resistance to alkali, acid, salt, corrosive gases, fog, and oxidants.
These resins are durable and offer long-term corrosion protection, making it an ideal top coating for offshore structures, ships, and harbor machinery.
Vinyl Resins are also known as modified alkyd resins that are durable, gloss, and hardness much superior to oleoresin coating.
The mechanical properties and good adhesion this coating provides makes it the best coating agent in offshore steel structures such as production decks.
Subsea Industries
Some of the subsea industries that tackle the issue of subsea corrosion regularly include:
- Drilling and Well Services
- Oil and Gas Exploration
- Underwater mining
- Undersea geology
- Offshore wind power industries
Approved Subsea Coating Applicators
When dealing with the issues of subsea corrosion, it is important to address the problem with the assistance of approved subsea coating applicators. Having approved and licensed subsea coating applicators will:
- Lessen direct and indirect costs of subsea corrosion
- Guarantee high quality work that meets international standards
- Provide adequate technical knowledge of subsea corrosion process and the proper ways to combat it
- Apply only the best (safe and tested) subsea corrosion protection
With Cor-Pro, clients will get superior service from its highly trained and approved coating applicators. Aside from quality work, clients will also get the Cor-Pro Gold Standard,” the highest standard of work in the corrosion industry.
With Cor-Pro’s Velocity Service, subsea industry clients will get the appropriate solution for any of their corrosion problems in a matter of hours after assessment.
Getting the subsea corrosion protection services from Cor-Pro means getting excellence as the company does not only comply with industry standards alone. The company continues to look for innovative ways to assist in mitigating corrosion. These methods are not only effective and environment-friendly but affordable, as well.
About Cor-Pro Systems
Known in Houston and nearby Gulf Coast areas as the leading provider of subsea corrosion protection services, Cor-Pro is a company that aims to lessen corrosion and its associated problems.
The company strives to improve personnel training and acquire top-of-the-line equipment to provide superior corrosion protection services at an affordable price.
Further, Cor-Pro works with various industry experts to develop safe and effective corrosion protection methods
Get Subsea Corrosion Protection Through Cor-Pro Systems, Inc.
If you have questions about our subsea corrosion protection or want to get a custom quote for your specific industry, contact us at 713-896-1091, or send us an e-mail at quotes@cor-pro.com.