Cor-Pro Systems, Inc. provides superior anti corrosion coatings services in Houston, Texas and nearby Gulf Coast areas.
Constant exposure to harsh chemicals causes metals to undergo a rapid rate of corrosion. As corrosion occurs, functionality and service life of equipments deteriorates. This means more unwarranted costs for the company and the industry.
In the recent study supported by NACE International, the United States spending on corrosion inhibitors almost doubled from $600 million in 1982 to 1.1 billion in 1998.
Additionally, a 2002 study by the U.S. Federal Highway Administration stated that corrosion costs several industries approximately $276 billion, which is about 3% of the nation’s GNP.
Anti corrosion coatings, when applied at the outset, can dramatically reduce these unnecessary economic losses.
Cor-Pro’s line of anti corrosion coatings coupled with their excellent service made the company the leading corrosion protection provider in Houston, Texas and nearby Gulf Coast areas.
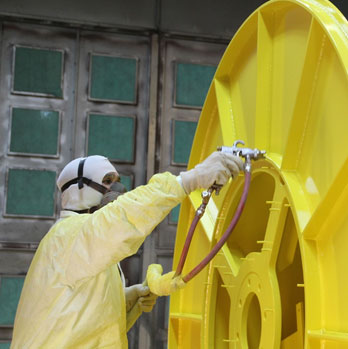
Cor-Pro Systems, Inc. corrosion management practices provides not only cost-effective anti corrosion coatings but also long-term solutions to any corrosion problem.
Learn more about Cor-Pro’s Anti Corrosion Coatings and choose the ideal methods suited for your corrosion problems.
What Are Anti Corrosion Coatings?
Anti corrosion coatings offer protection against deterioration caused by salt spray, moisture, oxidation, or constant exposure to a number of industrial and environmental chemicals.
Corrosion resistant coatings give additional protection for the metal surfaces and serve as a barrier that inhibits the contact between the corrosive materials and the chemical compounds.
Corrosion protection falls under three categories: a) Active Protection b) Passive Barrier Protection, and c) Cathodic Protection
A. Active Protection
When steel comes in contact with a primer combined with a reactive chemical compound, active corrosion protection ensues. This occurs because the reactive compound disturbs the normal formation of anodes present on the surface of the metal.
B. Passive Barrier Protection
On the other hand, passive barrier protection functions by coating the metal with corrosion protection system that makes a tight barrier to eliminate exposure to water, oxygen, and salt (ions). The lower the permeability of the anti corrosion coatings, the superior is the protection. For instance, chlorinated rubbers and two-pack epoxy coatings satisfactorily applied at high film builds gives the best corrosion protection using the passive barrier protection.
C. Cathodic Protection
A reaction between two different metals offers protection against corrosion. Cathodic protection through the use of sacrificial anodes, usually zinc, is one of the most commonly applied anti corrosion protection. The preference for zinc is secondary to the metal’s slower corrosion rate compared to other metals. However, it is still important to note that there would be an increased rate of corrosion in the presence of ions like chlorides in coastal locations.
C.1. Metallic Coatings
A number of metallic coatings are ideal for application to ferrous and non-ferrous substrates not only to stop the corrosion process but also to provide a decorative finish to the metal.
The specific coating material to use depends on the extent of the corrosive agents present in the surrounding environment of the metal – the severity of the wear and abrasion and the degree of visibility of the metal in service.
Application of metallic coatings can be through:
- Mechanical plating
- Electroplating
- Hot dipping
- Electroless
C.2. Electrocoating (E-Coating)
The process of e-coating involves the use of electrically charged particles deposited out of a water suspension to efficiently coat a conductive part. The process uses a coating tank with temperature control and circulation and filtering equipment.
Electrocoating, likewise, requires the use of a coating binder, pigment, and additives with an electrical charge. The following then migrate through the water to the surface under the influence of an electric field. These charged components give up their charge once they reach the part that causes the coating materials to drop out of the water suspension. They coalesce as the part coating surfaces.
A zinc or iron phosphate treatment enhances the electrocoating.
C.3. Organic Coatings
Organic coatings, such as paint, are a cost effective anti corrosion coating method. These coatings serve as a barrier to an electrolyte or a corrosive solution. They function by retarding the movement of an electrochemical charge from a corrosive solution towards the metal under the organic coating.
Coating thickness of the auto deposition film depends on the time and temperature. At first, the deposition process is rapid, but it slows down as the film starts to form.
Metals with tubular shape or those that have intricate designs are best coated by this process.
Benefits Of Anti Corrosion Coatings
Coatings with anti corrosion properties allow metals to acquire the longest possible service life. At present, a number of corrosion protection coatings are available to solve any corrosion issue
Industries that benefit from this corrosion protection method include:
- Energy Exploration
- Energy Services
- Fabrication
- Heavy Equipment
- Marine
- Military
- Petrochemical
- Processing/Refining
- Production
- Structural Steel
- Subsea Equipment
- Transportation
- Waste Treatment
Anti Corrosion Coatings By Cor-Pro Systems, Inc.
Cor-Pro Systems, Inc. brings almost three decades of expertise to the application of anti corrosion coatings, together with its 150,000 square foot facility manned with highly trained personnel ready to provide superior service that meets the “Cor-Pro Gold Standard.”
Cor-Pro provides anti corrosion coatings through:
- Epoxy Coatings
- 1-Hour Cure Epoxies
- Urethane Coatings
- Zinc Primers
- Enamels
- Thermal-Cured Thin Film (Xylan, Ceramic, Metallic, Thin Film Epoxy Moly, etc)
- Wear-Resistant Coatings
- High Temperature Coatings
- Abrasive Blasting (complete line of abrasive media available)
- Alternative profile achievement for areas not allowing blast.
Cor-Pro Systems, Inc is OHSAS 18001:2007 and ISO 9001:2008 certified. Both certification conferred by Verisys Registrars.
About Cor-Pro Systems
For 27 years, Cor-Pro serves its clients with only the best anti corrosion coatings that help equipments from various industries have longer service life with wider maintenance intervals.
Furthermore, Cor-Pro works with various organizations to undertake research and development that will help various industries to gain in-depth understanding of the corrosion process and the methods on how to prevent and stop it.
Getting anti corrosion coatings from Cor-Pro Systems is synonymous to getting an affordable and reliable corrosion protection.
Get Superior Anti Corrosion Coatings Through Cor-Pro Systems, Inc.
If you have questions about our anti corrosion coatings or want to get a custom quote for your particular corrosion protection need, contact us at 713-896-1091, or send us an e-mail at quotes@cor-pro.com.
Explore our Velocity Service page to know more about our custom anti corrosion coatings and other corrosion protection systems.