Cor-Pro Systems provides superior anti corrosion paint services in Houston, Texas and nearby Gulf Coast areas.
Corrosion protection is not just about the application of protective paints. It involves careful planning that starts with the identification of the anti corrosion paint to use, its effectiveness and suitability to the particular substrate.
When choosing an appropriate corrosion protection method, it is crucial to consider the type of corrosive environment the equipment is subject for exposure.
It is important to note that not all anti corrosion paints are applicable to use in all types of service exposures. An anti corrosion paint may be specific for certain equipment and environments only.
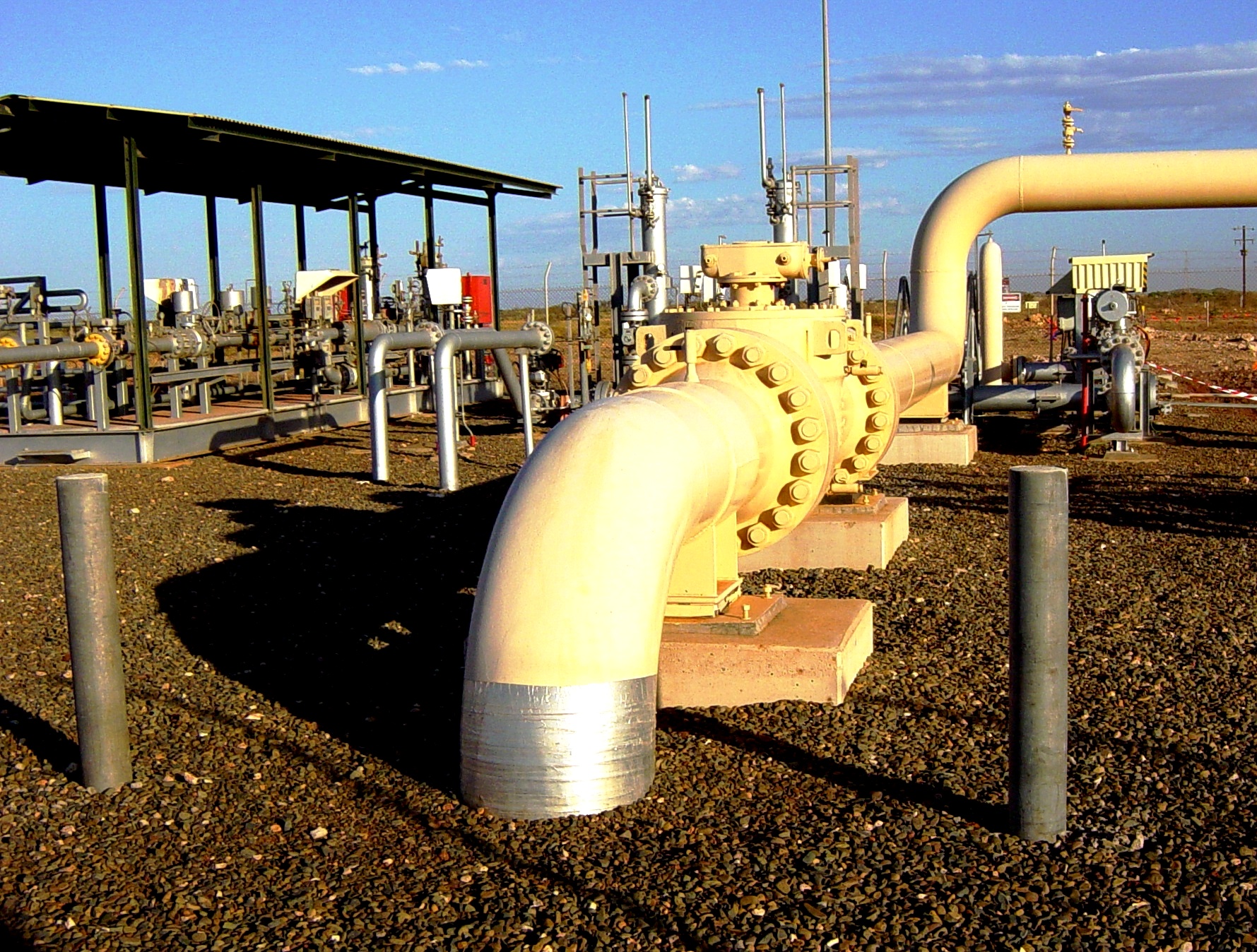
Anti corrosion paint should be compatible with the substrate material, its composition, and environmental condition in the field.
Cor-Pro Systems knows that corrosion is a serious problem that causes tremendous damages to different industries. It is the company’s mission to properly identify corrosive agents and provide appropriate solutions without additional cost.
The company dedicates a large part of their resources to further enhancing their knowledge, methodology, and application of anti corrosion paints to help mitigate the negative effects of corrosion.
Read about Cor-Pro’s Anti Corrosion Paint, the criteria for choosing a specific coating, and the preparations needed to achieve an effective protective barrier, and find out the proper corrosion protection system best
Anti Corrosion Paint and Service Exposures
Anti corrosion paint is ideally applied to protect solid metal surfaces and, in some occasions, various non-metals. Corrosion engineers are continuously developing different types of anti corrosion paints for various kinds of service exposures.
Environmental exposure has a great impact on the effectiveness and suitability of an anti corrosion paint.
Below is a list of the factors that corrosion engineers consider to effectively develop a suitable anti corrosion paint.
- Corrosive contaminants (indoor and outdoor)
- Condensation, humidity, splash exposure
- Soil chemistry (presence of acids, alkalis, and reactive salts), moisture, and electrical resistance
- Freshwater and saltwater exposure (partial, complete, fluctuating immersion)
- Reactivity of product type for transportation, handled or processed, and the associated hazard of leaks.
- Proximity to high voltage lines, cathodic or anodic protection, grounding stations, or railway stations that may cause stray currents
- Range and peak levels of temperature (fog, snowfall, storm, radiation, and UV exposure)
- UV radiation exposure, solvents, and sunlight
- Exposure to reactive to alkaline and acidic substances, sewage, and acid rain
- Projected lifespan of project operation, if any
- On site conditions that may affect surface preparation, priming, coating, and curing process
Anti Corrosion Paint: Different Types Of Application
Metallic Coatings
Metal coatings offers durable barrier against most types of corrosive substances. However, even minute defects on the surface can cause localized corrosive failure. Metal coatings as an anti corrosion paint is usually used as a decorative coating as well.
Application may be through:
- Electroplating
- Hot dipping
- Mechanical plating
- Thermal Spray
Non-Metallic Coatings
Majority of non-metallic anti corrosion paint offer protection through an insulating barrier that is impermeable by moisture and electrolytes that cause corrosion. Solvent, pigment, and resin comprise these non-metallic, liquid paints.
Solvent
The solvent functions to disperse and dissolve the resin material that serves as the strength of the paint coating. The solvent provides adequate adhesion, ease of application, and overall effectiveness.
Resin
This is the film forming component that provides protection against corrosion. This is why most paint coatings go by the name of the resin used.
Pigment
This serves as the second solid component of the anti corrosion paint coating. This provides the opacity need to stop an organic substance to sunlight exposure. Pigments also serve to enhance adhesion, weather resistance, color, and reduction of moisture ingress.
Resin and pigment stays on the surface when the solvent undergoes volatilization, and therefore determines the coat film thickness.
Classification Of Non Metallic Anti Corrosion Paint
Non-Metallic paint coatings, based on the mechanism of action, may be classified as:
Barrier Coatings
This type of anti corrosion paint coating forms a physical and insulating barrier that prevents the corrosive elements to come in contact with the substrate. Example: Coal tar epoxy coatings.
Galvanic Coatings
These coatings are rich in zinc content that serves as a sacrificial coating to a ferrous substrate. Galvanic coatings must be directly applied onto the substrate.
Inhibitor Coatings
Inhibitor coatings work by releasing a chemical by the pigment. This chemical then interferes with the electrolyte and disrupts electrochemical reactions. One example of inhibitor coatings that use this mechanism are chromate-type pigments.
Generic Polymer Coatings
Some of the generic anti corrosion paint commonly used in corrosion protection include:
- Alkyd Coatings: Based on modified natural oil, these are effective as a primer for atmospheric environments. They are not suitable for alkaline substrates like concrete.
- Acrylic Coatings: Eco-friendly, water-based and appropriate for use in outdoors with significant sunlight exposure. They can be applied as top coat or as a primer and best for moderate to high temperatures.
- Amine Epoxy: Highly resistant to acids, alkalis, and solvents. However, it is quite sensitive to moisture, temperature, and sunlight, and is hence used for underground coatings.
- Bitumen-Based Coating: Has high resistance to moisture but sensitive to solvents. Generally used for aluminum and ferrous surface protections.
- Coal Tar Epoxy: No moisture and chemical resistance and becomes brittle with time. Suitable for application to tank lining, immersion service, and industrial maintenance coating. Coal tar epoxy with glass filament reinforcement works for environments with high temperature.
- Epoxy Coal Tars and Urethanes: Ideal for large-diameter pipeline coating in petroleum industry.
- Extruded Polyolefin Systems: Generally used for pipes up to 24 inches in diameter. Improvements in adhesion and increased availability of polypropylene for application in environments with wide and high temperatures make the system popular and effective since it can provide holiday-free coatings.
- Fusion-Bonded Epoxy: Ideal for immersion and buried services in environments with moderately high temperatures.
- Moisture-Cured Urethane: Ideal for damp environments. Its advantage is it is customizable pigment formulations that match the service exposure.
- Polyamide Epoxy: Resistant to water and salt solutions, but not appropriate for other chemicals. Best for buried and immersion services.
- Urethane and Polyurethane: Suitable for environments with atmospheric exposure and for substrates that function in fluctuating immersion operations.
Anti Corrosion Paint From Cor-Pro Systems, Inc.
Cor-Pro offers suitable anti corrosion paint for any service exposure. Corrosion protection from Cor-Pro Systems will give your business:
- Longer service life of equipment by as much as 250%, which means more savings.
- Continuous operation that ensures smooth flow of business that translates to profit.
- Longer maintenance intervals, which means lower maintenance cost.
- Lower corrosion-related accidents that releases your company from legal and environmental liabilities.
Cor-Pro’s unparalleled dedication to its clients enabled the company to develop effective corrosion protection systems. These are applications customized by our experts, depending on the specific corrosion problem.
About Cor-Pro Systems
Cor-Pro recently received its OHSAS 18001:2007 and ISO 9001:2008 certification through Verisys Registrars. These certifications are testaments to the company’s continuous drive for excellence.
Cor-Pro and its close to 30 years of providing top-of-the-line anti corrosion paint and coatings to various industries helped the economy tremendously by reducing the direct and indirect cost caused by corrosion.
The company spends ample time to research and development and information drives to further increase awareness about corrosion, its adverse effects, and the effective ways to prevent it.
Get High Quality Anti Corrosion Paint Through Cor-Pro Systems, Inc.
If you have questions about our anti corrosion paint or want to get a custom quote for your particular corrosion protection need, contact us at 713-896-1091, or send us an e-mail at quotes@cor-pro.com.
Check out our Velocity Service page to know more about our available anti corrosion paint and other corrosion protection systems.